If you're tinkering with a car or constructing an appliance, then you may be interested in using a ceramic part. This material has a number of advantages, including high melting points and high hardness. In addition, some ceramic parts are harder than titanium, have excellent oxidation and corrosion resistance, and conduct electricity better than copper. Furthermore, ceramics are environmentally friendly and can absorb toxic waste, purify water, and reduce pollution.
A key characteristic of a ceramic part is its ability to withstand high compression loads, but this characteristic is often limited by its size. Thicker components may shrink by up to 30%, which can make their shapes unmanageable. To improve ceramic parts' mechanical performance, consider design tips. One way to simplify a ceramic part is to modify the non-ceramic part's form. The use of modular designs, for example, eliminates the need for diamond grinding and increases its mechanical properties.
A ceramic part can be manufactured in a number of ways, and the main process is known as machining. The process is a multistep one, and includes milling, casting, and injection molding. Slip casting is a mold casting method that works well for mass production of sanitary ware. Hot isostatic pressing is another method used to manufacture ceramic parts. Injection molding and extrusion molding are two other methods for creating ceramic parts.
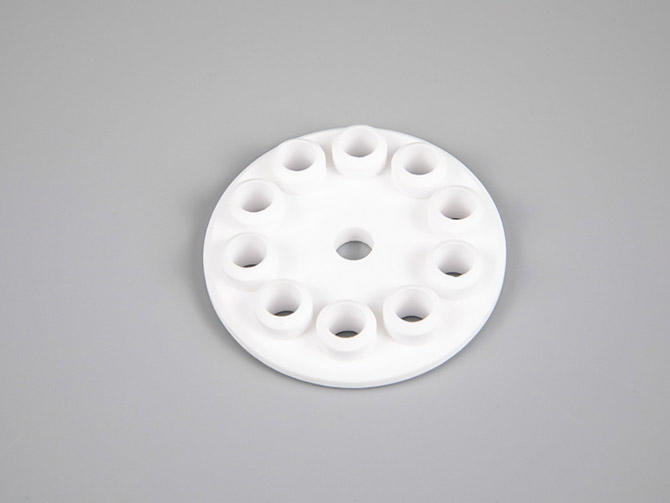
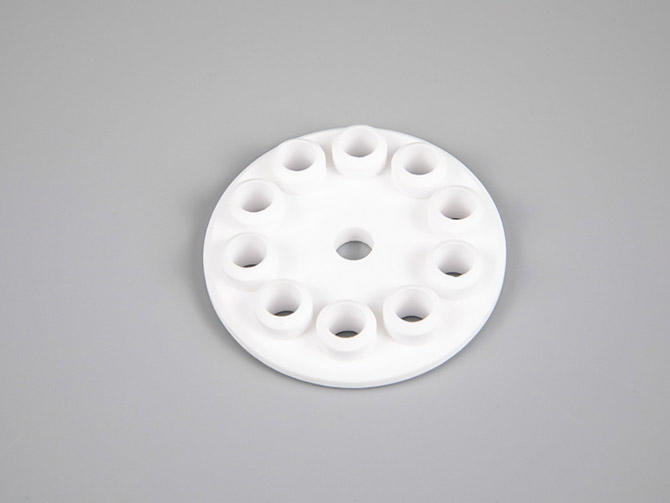
The basic process of creating a ceramic part begins with the mixing of clay with earthen elements or powders. Then, the clay is formed into the desired shape and fired in a high temperature oven. Some ceramic parts have decorative coatings or are waterproof. The process used to create a ceramic part differs by end use. If you're looking to buy a ceramic part, you can begin your search by browsing online. They have many uses.
For example, alumina ceramics can be used to make high-temperature components, such as circuit boards. The material has exceptional chemical resistance, corrosion resistance, and high hardness. These properties make it an excellent material for electrical components. Alumina ceramics can be used in everything from power sources to medical equipment. Besides these uses, alumina ceramics are economical and versatile. They are also highly resistant to abrasion and rust.
While ceramics are not metallic, they are essential for daily life. Ceramic engineers design processes that produce ceramic products and look for different applications. Whether a ceramic part is needed for a car engine or for a refrigerator door, a ceramic part can be used in virtually any application. It can even be used to build a solar panel. So, you'll never be without a ceramic part! If you're looking for a high-quality ceramic part, look no further.
A ceramic part is typically made of several types of materials. Alumina is a mineral that is a form of carbon. Its density make it a perfect material for automotive parts. However, alumina is often mixed with other materials before the forming process. The combination of different substances determines the grade of ceramics. For example, alumina is blended with other materials and alumina is mixed with these substances to make a granulated powder. Alumina is also used in ceramic dough feedstock and spray-dried powder.