Advanced technical ceramics (ATCs) are materials with high temperature, hardness, and electrical resistance. These materials are often used as substitutes for metals, polymers, and refractory materials. The characteristics of these materials make them ideal for high-tech applications. Some of the alumina ceramics in today's electronics include sensors in cars and computer chips. These materials can resist mechanical stress and contribute to increased efficiency.
Ceramic components with high strength-to-weight ratio are used in many applications. They are lightweight and exhibit excellent insulative properties. They can be used in catalyst carriers and diesel particulate filters, which improves their life-span and durability. Moreover, new compositions have improved the thermal and electrical properties of these components. They can also offer good toughness and flexibility in pore structures.
The process of manufacturing an alumina ceramic component begins with alumina powder, which is generally a form of aluminum. Alumina powders are typically of a particle size of one to five microns, although any suitable alumina powder will fit within this range. When this powder is combined with a binder and alumina powder, the result is a composite material that exhibits excellent flexural strength and high thermal shock resistance.
Another advantage of reaction-bonded high alumina ceramics is the ability to process alumina-based insulation components at reduced temperatures and with significantly less phosphate-based reagents. This new process can be used to produce alumina-based insulating components and offers improved thermal and electrical insulation performance in harsh environments. This process can also be used to produce net-shaped and net-sized components, eliminating post-machining. The overall cost-effectiveness of the proposed material system is significant when compared to other comparable high alumina insulation materials.
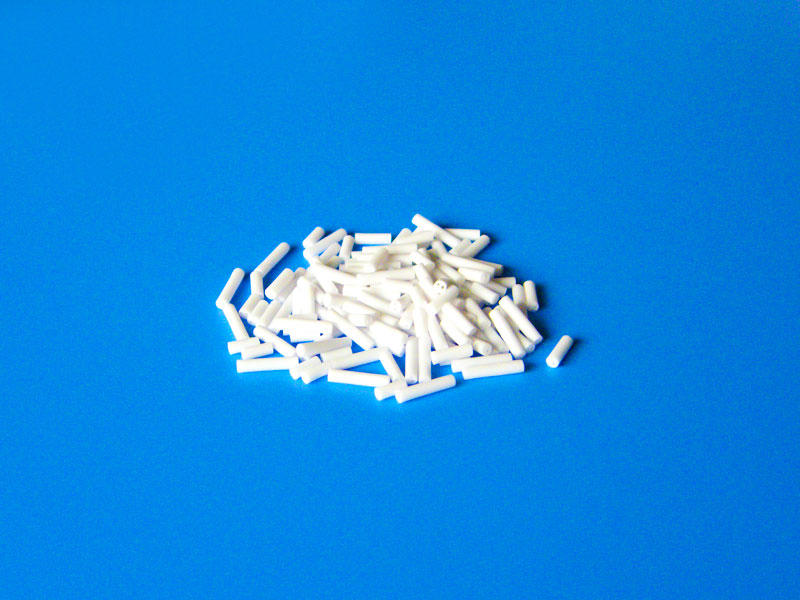
Alumina is an extremely versatile material, allowing it to serve as an excellent electrical conductor and electrical insulator. Alumina is also remarkably hard and wear-resistant, making it a great choice for applications that require high temperature brazing. This material is also used in high-voltage components, including laser equipment and semiconductors. It is even possible to mold alumina into body armor. So it is possible to use it in many ways and it will remain a useful part for decades to come.
Despite being durable, the alumina ceramic component may not be completely infallible. Several studies have concluded that alumina ceramics have low fracture rates. Several studies have found that only one in a thousand implanted components fracture within five years. Therefore, precise quantification of fracture rates is difficult. Nevertheless, CeramTec reports that the fracture rate of an alumina-based hip component is one to three per 10,000. However, some studies have reported higher rates.
Alumina ceramics are the most common type of advanced ceramic materials. Alumina is a naturally occurring mineral that contains both aluminium and oxygen molecules. This substance is also known as aluminium oxide. Other forms of alumina occur in nature. Several methods are used to manufacture alumina ceramics, including precision grinding and laser machining. Its high hardness makes it a desirable material for a variety of applications, including electronics.