Alumina ceramic firing technology Electric furnaces are widely used as heating devices for firing. In addition to normal pressure sintering, that is, pressureless sintering, there are also hot pressing sintering and hot isostatic pressing sintering. Although continuous hot pressing sintering increases the output, the cost of equipment and molds is too high, and the length of the product is limited due to the axial heating. Hot isostatic pressing uses high temperature and high pressure gas as the pressure transmission medium, which has the advantage of uniform heating in all directions, and is very suitable for the sintering of products with complex shapes. Due to the uniform structure, the material properties are improved by 30-50% compared to cold-pressed sintering. It is 10-15% higher than general hot pressing sintering. Therefore, at present, some high value-added alumina ceramic products or special parts for national defense and military industries, such as ceramic bearings, mirrors, nuclear fuel and gun barrels, use the hot isostatic pressing method.
Alumina ceramic production process 1. Powder preparation: The alumina powder entering the factory is prepared into powder materials according to different product requirements and different molding processes. The powder raw material formed by the hot pressing process does not need to add a binder. If semi-automatic or fully automatic dry pressing is used, the powder has special technological requirements. It is necessary to use the spray granulation method to process the powder to make it appear spherical, so as to improve the fluidity of the powder and facilitate automatic filling of the mold during molding. wall.
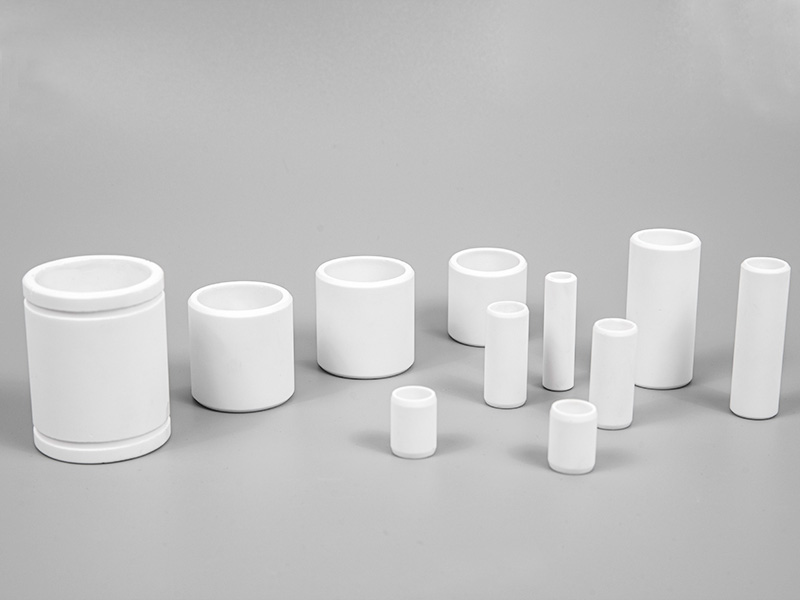
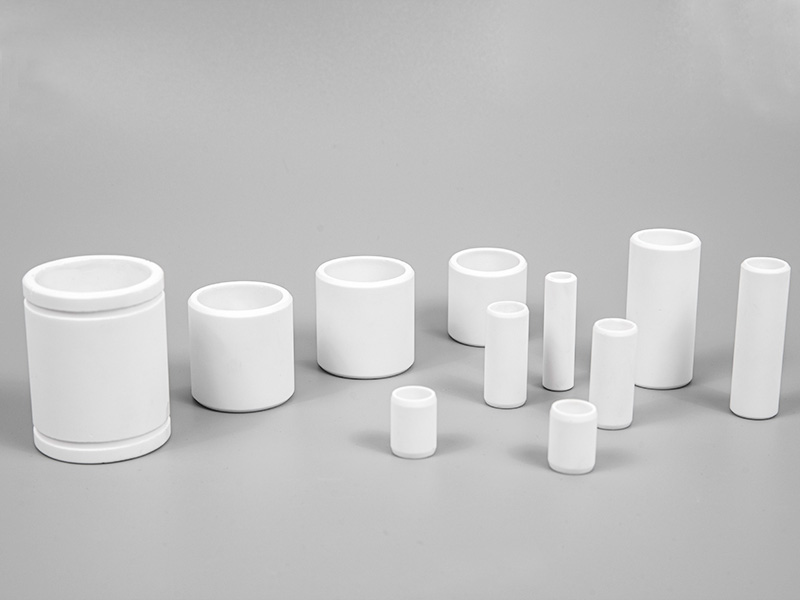
2. Forming method: The forming methods of alumina ceramic products include dry pressing, grouting, extrusion, cold isostatic pressing, injection, casting, hot pressing and hot isostatic pressing. In recent years, pressure filtration molding, direct solidification injection molding, gel injection molding, centrifugal grouting and solid free molding have been developed at home and abroad in recent years. Products with different product shapes, sizes, complex shapes and precision require different molding methods. In the finishing and packaging process of alumina ceramics, due to the high hardness of alumina ceramic materials, it is necessary to use harder grinding and polishing brick materials for finishing. . Such as SIC, B4C or diamond and so on. It is usually ground by grades from coarse to fine abrasives, and the final surface is polished. Generally, Al203 powder or diamond paste with a micron size of <1μm can be used for grinding and polishing. In addition, laser processing and ultrasonic processing grinding and polishing methods can also be used.
Our company has several sets of production equipment for alumina and zirconia ceramics, as well as professional rough grinding and precision machining equipment. It can perform rough grinding, precision machining and polishing of plane, inner hole and outer circle for various types of alumina and zirconia ceramic products. It can be produced and processed according to the samples provided by customers; it can also be produced according to the production drawings provided by customers.