Oxide ceramics is a ceramic material with AL2O3 as the main crystal phase. Its alumina content is generally between 75%and 99%. It is used to classify the content of alumina in the ingredients. The alumina content is "75%porcelain" with an alumina content of about 75%, and the content of 99%is "99%porcelain". Gangyu#183; Mo Lai Shi porcelain has an aluminum alumina content of more than 70%, and the alumina content of Gangyu porcelain is more than 90%. Generally, Gangyu Porcelain and Gangyu#183; Mo Lai Shi Porcelain becomes alumina porcelain. The manufacturing methods are also different according to different types, different performance requirements, and different shapes, size and thickness of the product, but the manufacturing methods are also different, but the following process is generally: pre-burning alumina-because industrial alumina raw materials are usually Al2O3.
Therefore, before the oxidation LV powder is used to make alumina ceramics, the oxide LV powder must be pre -burned, or it is called a burning.
In practical applications, it is widely used because alumina has high hardness and density. Its heroic hardness is 9, which is slightly lower than diamonds. The volume density is generally more than 3.5 g/cm³, and some can reach 4.0g/cm³. Alumina ceramics are divided into 99 porcelain, 95 porcelain, 90 porcelain, 85 porcelain and other varieties according to the content of AL2O3. Among them, 99 alumina ceramics materials are used to make high temperature, stove -resistant furnace pipes and special wear resistance materials, such as ceramic bearing, ceramic sealing sealing Pieces, etc.; 95 alumina ceramics are mainly used as corrosion -resistant and wear -resistant components.
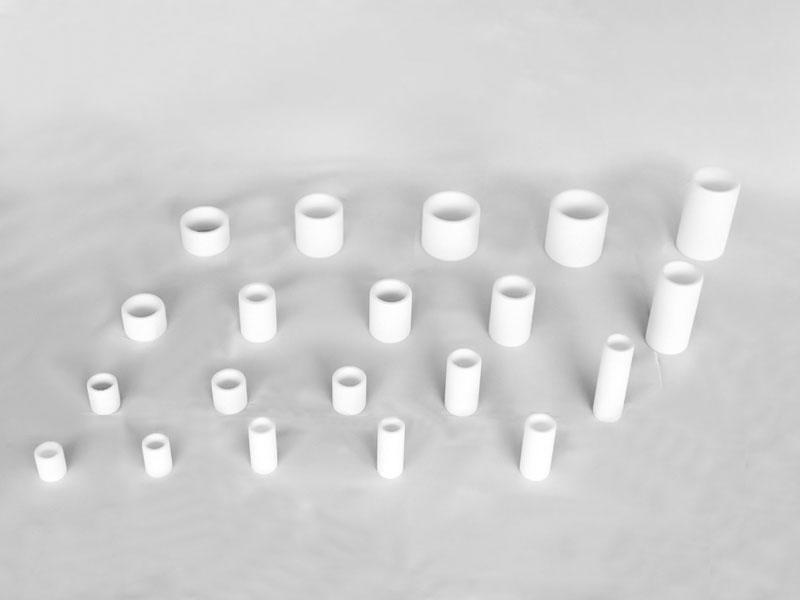
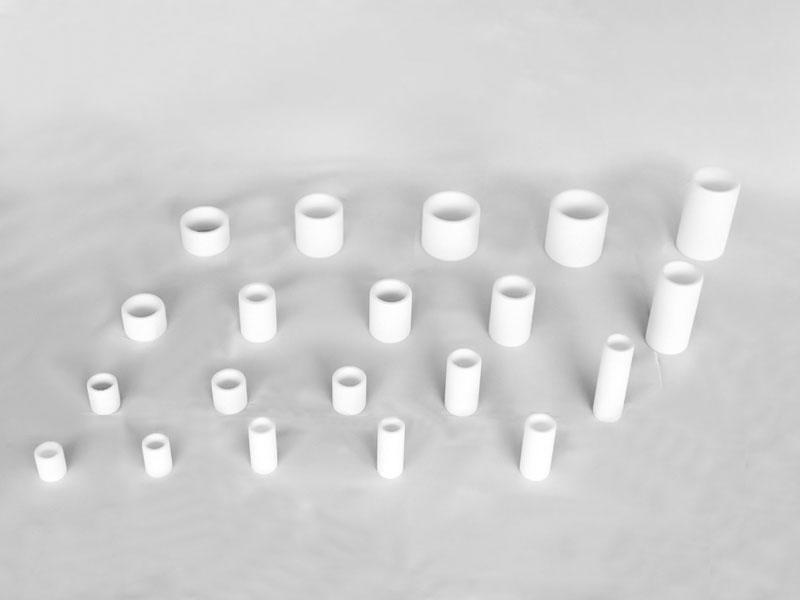