With the continuous development of society, alumina ceramic structural parts are widely used in electronic appliances, machinery, chemical industry, metallurgy, aerospace and other industries due to their excellent performance. Cost, how to reduce the sintering temperature of alumina ceramic structures?
First understand the reasons why alumina ceramic structural parts need high temperature sintering:
Due to the characteristics of alumina's own cationic charge, small radius, and strong ionic bonds, its lattice energy is large and its diffusion coefficient is low. The high temperature produces less liquid phase, and its sintering is mainly completed by the recrystallization of crystals, resulting in a generally high sintering temperature of alumina ceramics.
High temperature means high energy consumption and high cost, so reducing the sintering temperature of alumina ceramics is of great significance to enterprise production.
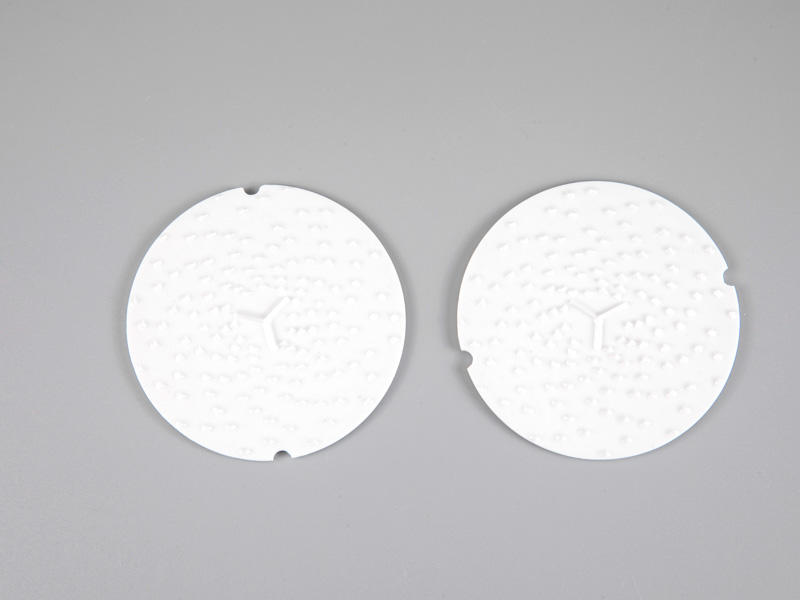
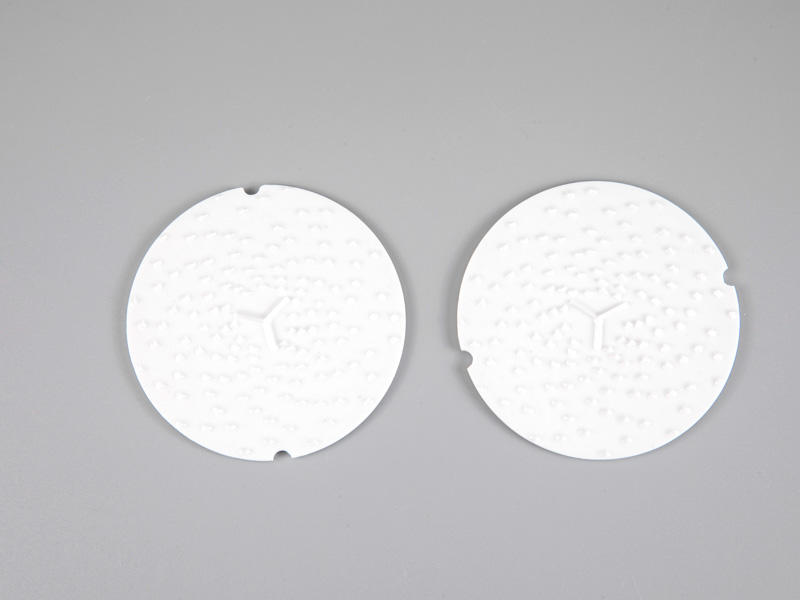
So, how to reduce the sintering temperature of alumina ceramic structures:
1. Reduce powder particle size
Studies have shown that the finer the powder particles, the more defects, the greater the activity, which can promote sintering and the higher the strength of the ceramic. When the particle size of the powder is reduced to 20 nm or less, the sintering temperature of the ceramic can be reduced to 1000° C. or lower.
The preparation of ultra-fine powder can reduce the sintering temperature, but the preparation cost of the powder is too high, and the shape of the sintered body is difficult to control, so it is not easy to be adopted by enterprises.
2. Add sintering aids
In the production process of alumina ceramics, sintering aids are often added to reduce the sintering temperature of alumina ceramics by changing the formula design. According to their different mechanisms of promoting the sintering of alumina ceramics, they can be divided into two categories: additives that form new phases or solid solutions and additives that generate liquid phases.
3. Using special sintering process
Special sintering process refers to the addition of sintering driving force during the sintering process of alumina ceramics to promote the densification of ceramics. Nowadays, the common special sintering processes mainly include hot pressing sintering, hot isostatic pressing sintering, microwave heating sintering, microwave plasma sintering , spark plasma sintering, etc. In addition, vacuum sintering, atmosphere sintering, electric field sintering, ultra-high pressure sintering, activation sintering and activation hot pressing sintering can also reduce the sintering temperature, but because the cost is too high, it is generally not considered.
Hot pressing sintering: Unidirectional pressure is applied to the sample at high temperature to promote full densification of the ceramic. For pure alumina ceramics, conventional sintering requires a temperature above 1800 °C; while 20MPa hot-pressing sintering requires only 1500 °C.
Hot isostatic pressing sintering: sintering by applying pressure to all directions of the ceramic body at the same time, reducing the sintering temperature of the ceramic, and at the same time, the sintered ceramic has a uniform structure and good performance.
Microwave heating method sintering: using the interaction between microwave and ceramics, the interior and surface of ceramics are sintered at the same time due to the dielectric effect.
Microwave plasma sintering: Compared with conventional sintering, the sintering temperature can be reduced by 200°C under the same conditions, and the sintering speed is fast, the grain size is small, and the mechanical strength is high.
Spark plasma sintering: The instantaneous high temperature field generated by pulse energy and pulse pressure is used to realize the spontaneous heating of the crystal grains inside the ceramic to activate the crystal grains. Because of this sintering method, the temperature rises, the temperature is fast, and the holding time is short, which inhibits the growth of crystal grains. , Shorten the preparation cycle of ceramics and save energy.
The above methods for reducing the sintering temperature of alumina ceramics are not independent, and they play different leading roles under different conditions. In specific production, they can be used in combination with each other in order to obtain ceramic products with the best performance.